HYDRAULIKA I PNEUMATYKA, ZESZYT 5/2002________22
TADEUSZ KRET
IRENEUSZ MADEISKI
ROMAN WOJTKIEWICZ
Układ hydrauliczny zmodernizowanej prasy wulkanizacyjnej.
Wprowadzenie
W roku 1999 w KWB Turów przeprowadzono modernizację "starej"
dwudziestoletniej prasy hydraulicznej o nacisku 43 MN.
Wynikiem dokonanych zmian była bardzo znaczna poprawa parametrów technicznych prasy co
skutkowało poprzez:
- jakość produkowanych taśm,
- warunków BHP i ergonomii obsługi
- niezawodności pracy prasy.
Tak duża poprawa parametrów pracy prasy była zapewne powodem podjęcia przez Inwestora
modernizacji układów hydraulicznych i układu sterowniczego kolejnej prasy
wulkanizacyjnej zamontowanej przez firmę niemiecką w roku 1986.
Prasa ta o nacisku 19 MN jest ogrzewana i chłodzona olejem z niezależnego urządzenia
umieszczonego w pomieszczeniach hali obok. Zadaniem urządzenia grzewczo-chłodzącego
jest dostarczanie do prasy oleju grzewczego o odpowiednich parametrach.
Komunikacja między obydwoma urządzeniami odbywa się za pomocą sygnałów dwustanowych:
- ze strony prasy, żądanie:
- włączenia ogrzewania,
- włączenia chłodzenia,
- otwarcie zaworu regulacyjnego
(przy zbyt niskiej temperaturze płyt stołu zamknięcie tego zaworu),
- ze strony urządzenia grzewczo - chłodzącego sygnału o osiągnięciu gotowości do pracy.
Opis układu hydraulicznego
Na rys.1 przedstawiono schemat układu hydraulicznego prasy wulkanizacyjnej.
Pompa M1 zasilana silnikiem elektrycznym 18,5kW napędza prasę podczas ruchów szybkich
(zamykanie prasy) przy niskim ciśnieniu oleju.
Pompa M2 zasilana silnikiem 22kW napędza prasę podczas domykania prasy.
Podczas wulkanizacji poprzez regulator przepływu [21] dozuje olej do siłowników Z1.
Pompa M3 (2,2kW) pompuje w sposób ciągły olej poprzez dokładny filtr (10mm) zamontowany równolegle w układzie hydraulicznym.
Siłowniki główne nurnikowe Z1 (8 szt.) służą do zamykania prasy, otwieranie prasy następuje pod ciężarem płyty dolnej.
Siłowniki Z2 (4 szt.) podwójnego działania służą do odklejenia taśmy wulkanizacyjnej od górnej płyty grzewczej podczas otwierania prasy.
Siłowniki Z3 (2 szt.) służą do dosuwania listew bocznych ograniczających szerokość wulkanizowanej taśmy.
Rys.2 - cyklogram pracy prasy
- przedstawia podstawowe zależności pomiędzy ruchami poszczególnych grup siłowników,
zmiennych ciśnień w układzie głównym oraz temperatury płyt grzewczych prasy.
System sterowania
Do sterowania i sygnalizacji wykorzystuje się w prasie swobodnie programowalny sterownik SIMATIC S5-115U,
operatorski terminal TD27-6 (monochromatyczny z ekranem dotykowym) oraz pulpity sterownicze.
Oprogramowanie terminala zawiera 7 ekranów użytkowych. Na każdym ekranie są utworzone odpowiednie przyciski funkcyjne i sterujące.
Dotknięcie przycisku powoduje zamkniecie ekranu lub uruchomienie funkcji opisanej na przycisku.
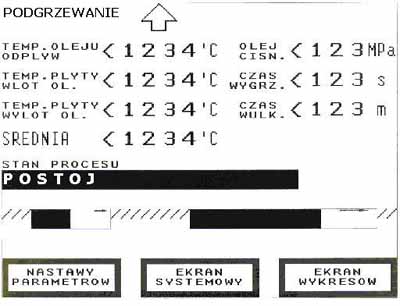
Rys.3 - Ekran główny
Po załączeniu zasilania prasy pojawia się ekran główny (podstawowy) pokazujący w sposób schematyczny przebieg temperatury i ciśnienia
wulkanizacji.
Ekran ten zawiera wszystkie podstawowe informacje niezbędne do oceny prawidłowości procesu wulkanizacji.
Przebieg procesu wulkanizacji, można śledzić na bieżąco lub odczytać po zakończeniu procesu na kolejnym ekranie.
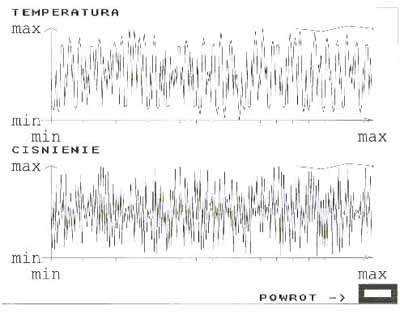
Rys.4 - Ekran z przebiegiem procesu wulkanizacji.
Cały cykl technologiczny pracy prasy został podzielony na poszczególne stany pracy prasy:
- Stan POSTÓJ
- prasę można załadować jedynie w stanie postoju. Stan ten oznacza, że prasa jest otwarta (krańcówką 1B1E) a listwy boczne są rozsunięte
(1B5E; 1B5/1E ). Po załadowaniu prasy, można ją zamknąć.
Warunki zamknięcia są następujące:
- opuszczony mechanizm podnoszenia taśmy,
- ustawienie listw bocznych we właściwym położeniu.
Jeżeli warunki są spełnione system sygnalizuje, że można przejść do następnego stanu.
- Stan ZAMYKANIE
- powoduje załączenie pompy niskiego ciśnienia (1M1). Pompa pracuje do czasu zadziałania wyłącznika krańcowego A-B2E
("Prasa przymknięta") lub do uzyskania w obwodzie hydraulicznym ciśnienia ((czujnik analogowy 1B1) nastawionego w polu
"CIśN. WSTĘPNEGO ZACISKU" na ekranie "Parametry pozostałe".
Po osiągnięciu wyłącznika krańcowego lub nastawionego ciśnienia pompa wyłącza się.

Rys.5 - Ekran pozostałe parametry.
Stan POSTÓJ
- prasa powoli rozgrzewa się (rozgrzewanie odbywa się z kontrolą gradientu temp. najgorętszego punktu płyty prasy).
Stan NAGRZEWANIE
- po osiągnięciu temp. wygrzewania ("Parametry pozostałe" w polu "TEMP. WSTĘPNEGO WYGRZEWANIA") następuje wygrzewanie
taśmy przez czas nastawiony w polu "CZAS WYGRZEWANIA" (ekran "Parametry pozostałe").
Po odmierzeniu nastawionego czasu na pulpicie miga lampka przycisku "AUTO" - oznacza to gotowość do rozpoczęcia
automatycznego przeprowadzenia procesu wulkanizacji.
Stan WYGRZEWANIE
- po osiągnięciu temp. wygrzewania ("Parametry pozostałe" w polu "TEMP. WSTĘPNEGO WYGRZEWANIA") następuje wygrzewanie
taśmy przez czas nastawiony w polu "CZAS WYGRZEWANIA" (ekran "Parametry pozostałe").
Po odmierzeniu nastawionego czasu na pulpicie miga lampka przycisku "AUTO" - oznacza to gotowość do rozpoczęcia
automatycznego przeprowadzenia procesu wulkanizacji.
Stan GOTÓW DO ZAMKNIĘCIA
- prasa pozostaje przymknięta, temperatura utrzymywana jest zgodnie z wartością nastawioną
("Parametry pozostałe" w polu "TEMP. WSTĘPNEGO WYGRZEWANIA") aż do naciśnięcia przycisku "AUTO".
Stan NAGRZEWANIE 2
- naciśnięcie przycisku "AUTO" powoduje włączenie pompy wysokiego ciśnienia (M2) i zaciśnięcie prasy (siłowniki Z1) do wartości
nastawionego ciśnienia ( ekran "Parametry pozostałe", pole "CIŚNIENIE WSTĘPNEGO ZACISKU").
Prasa nagrzewa się aż do osiągnięcia temp. pierwszego odgazowania (pole "TEMP. I ODGAZOWANIA" na ekranie "Pozostałe parametry").
Ogrzewanie odbywa się z kontrolą gradientu temperatury najgorętszego punktu prasy.
Stan ODGAZOWANIE 1
- ciśnienie w prasie spada do wartości "CIŚN. MIN. ODGAZOWANIA" (ekran "Parametry pozostałe") i stan ten utrzymuje się przez 10 sekund.
Po tym czasie ciśnienie w prasie zwiększa się i prasa przechodzi do następnego stanu.
Stan NAGRZEWANIE 3
- ciśnienie w prasie zwiększa się do wartości nastawionej w polu
"CIŚNIENIE II ODGAZOWANIA" (ekran "Nastawy parametrów") i jest utrzymywane na tym poziomie aż do osiągnięcia przez płyty prasy
temperatury ustawionej w polu
"TEMP. II ODGAZOWANIA" (ekran "Parametry pozostałe").
Nagrzewanie odbywa się pod kontrolą gradientu temp. najgorętszego punktu prasy.
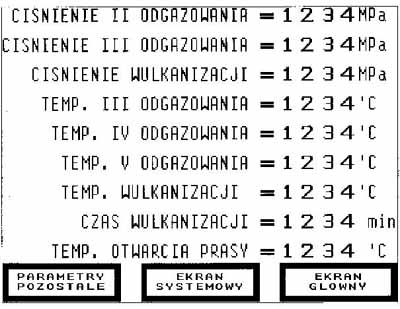
Rys.6 - Ekran "Nastawy parametrów".
Stan ODGAZOWANIE 2
- gdy oba warunki (temp. ciśnienie) są spełnione następuje drugie odgazowanie. Ciśnienie w prasie spada do wartości
"CIŚNIENIE MIN. ODGAZOWANIA" i stan ten utrzymuje się przez 10 sekund.
Stan NAGRZEWANIE 4
- po zakończeniu drugie odgazowania ciśnienie w prasie zwiększa się do wartości nastawionej w polu
"CIŚNIENIE II ODGAZOWANIA" (ekran "Nastawy parametrów") i jest utrzymane na tym poziomie aż do czasu osiągnięcia przez
płyty prasy temperatury ustawionej w polu
"TEMP. III ODGAZOWANIA" (ekran "Nastawy parametrów").
Stan ODGAZOWANIE 3
- proces odgazowania następuje po osiągnięciu temperatury ustawionej w polu
"TEMP. III ODGAZOWANIA" (ekran "Nastawy parametrów").
Stan NAGRZEWANIE 5
- po zakończeniu trzeciego odgazowania ciśnienie w prasie wzrasta do wartości nastawionej w polu
"CIŚNIENIE III ODGAZOWANIA" (ekran "Nastawy parametrów").
Aż do otwarcia prasy wartość ta jest utrzymywana automatycznie na jednym poziomie.
Gdy ciśnienie (skutkiem np. nieszczelności w układzie hydraulicznym) spadnie o wartość większą niż nastawiona w polu
"HISTEREZA CIŚNIENIA" załącza się zespół zaworów uzupełnienia wysokiego ciśnienia (1Y2V; 1Y1V; 1Y3V) aż do czasu powrotu
ciśnienia do wartości nastawionej.
Nagrzewanie odbywa się z kontrolą gradientu temperatury najgorętszego punktu prasy do czasu osiągnięcia temperatury IV
odgazowania ("TEMP. IV ODGAZOWANIA" na ekranie "Nastawy parametrów").
Stan ODGAZOWANIE 4
- warunkiem IV odgazowania jest osiągnięcie ustawionej temperatury. W przypadku wpisania w polu
"TEMP. IV ODGAZOWANIA" (na ekranie "Nastawy parametrów") wartości 200oC odgazowanie IV zostanie pominięte i prasa przejdzie do stanu
"NAGRZEWANIE".
Stan NAGRZEWANIE
- po zakończeniu IV odgazowania ciśnienie w prasie wzrasta do wartości nastawionej w polu
"CIŚNIENIE III ODGAZOWANIA" (ekran "Nastawy parametrów").
Prasa rozgrzewa się do temperatury V odgazowania.
Stan ODGAZOWANIE 5
- warunkiem V odgazowania jest osiągnięcie ustawionej temperatury. Gdy jest potrzeba pominięcia tego odgazowania
należy wpisać temp. 200oC w polu
"TEMP. V ODGAZOWANIA".
Stan NAGRZEWANIE
- po zakończeniu V odgazowania ciśnienie w prasie wzrasta do wartości nastawionej w polu
"CIŚNIENIE WULKANIZACJI". Prasa rozgrzewa się do temperatury wulkanizacji.
Stan WULKANIZACJA
- po osiągnięciu temperatury wulkanizacji ("TEMP. WULKANIZACJI" ekran "Nastawy parametrów") zaczyna się odmierzanie czasu
( pole "CZAS WULKANIZACJI" ekran "Nastawy parametrów"). Aktualny czas, można odczytać na ekranie głównym.
Temperatura płyt, utrzymywana jest wokół nastawionej temperatury wulkanizacji.
Stan CHŁODZENIE
gdy czas wulkanizacji zostanie odmierzony prasa przechodzi w stan chłodzenia. Do prasy jest kierowany strumień oleju chłodzącego.
Stan MOŻNA OTWIERAĆ
- osiągnięcie przez prasę temperatury nastawionej w polu
"TEMP. OTWIERANIA PRASY" (ekran "Nastawy parametrów") oznacza zakończenie cyklu wulkanizacji.
Układ sygnalizuje wówczas możliwość otwarcia prasy.
Odgazowanie dodatkowe
- jest możliwe po naciśnięciu przycisku na pulpicie po zakończeniu stanu
"ODGAZOWANIE 1" aż do końca stanu "WULKANIZACJA". Naciśnięcie tego przycisku spowoduje zmniejszenie ciśnienia w prasie do
wartości identycznej jak przy odgazowaniach automatycznych i trwa tak długo jak długo jest naciśnięty przycisk.
Po zwolnieniu przycisku ciśnienie wraca do poprzedniej wartości.
Awaryjne otwarcie prasy
- jest możliwe w każdym stanie i odbywa się przez jednoczesne naciśnięcie przycisków "ZAMYKANIE" i "OTWIERANIE".
Aktualny stan pracy prasy (pamięć procesu) jest wówczas kasowany i prasa przechodzi natychmiast do stanu "MOŻNA OTWIERAĆ".
Podsumowanie
Przeprowadzona modernizacja układów hydraulicznego i sterowniczego przyniosła natychmiastowe efekty w zakresach:
- Technologicznym
Dobór wzajemnych korelacji między zaciskami prasy, temperaturą, czasem i później właściwy przebieg procesu technologicznego
były powodem całkowitej eliminacji miejscowych przegrzań i niedowulkanizowań taśmy powstających w czasie procesu technologicznego.
Wada ta była związana głównie ze sposobem grzania prasy i z tym związanym nierównomiernym nagrzewaniem płyt prasy.
Wprowadzono w pamięć sterownika zarys głównych technologii (np. dla taśm z wzmocnieniem tekstylnym lub stalowym).
Regulacje nastaw technologicznych przedstawiono w postaci kilku progów dostępnych za pomocą haseł
(nastawy obsługi, dozoru średniego, wyższego, serwisu itp.).
Umożliwiono przegląd procesu po jego zakończeniu w postaci wykazu na panelu lub wydruku.
- Serwisowym
Systemowo zabezpieczono układy przed ekstremalnymi nastawami.
Wprowadzono sygnalizację awarii na panelu ze wskazaniem jej miejsca występowania.
- Obsługi i poprawy warunków BHP
Cała komunikacja i obsługa prasy w zakresie sterowania i podglądu parametrów technologicznych została sprowadzona do terminala
operatora i niewielkiego pulpitu sterowniczego.
Wszystkie kroki procesu, wykonywane są automatycznie za wyjątkiem tych, które wymagają oceny i działań obsługi.
Są one jednak tak zorganizowane, że sygnalizują każdy następny, miganiem lampki przycisku.
Obejście przez operatora tej procedury jest niemożliwe.
Wyżej przedstawione rozwiązania znalazły uznanie nie tylko wśród dozoru, ale także wśród obsługi prasy,
co zdaniem autorów jest bardzo ważne przy wdrażaniu nowoczesnych rozwiązań.
Inż. Tadeusz Kret i inż. Ireneusz Madeiski reprezentują firmę KRET I S-KA,
a mgr inż. Roman Wojtkiewicz pracuje w Instytucie Poltegor we Wrocławiu.
|